Bolton’s woodchip bioreactor: A green solution for nitrate reduction
July 23, 2025
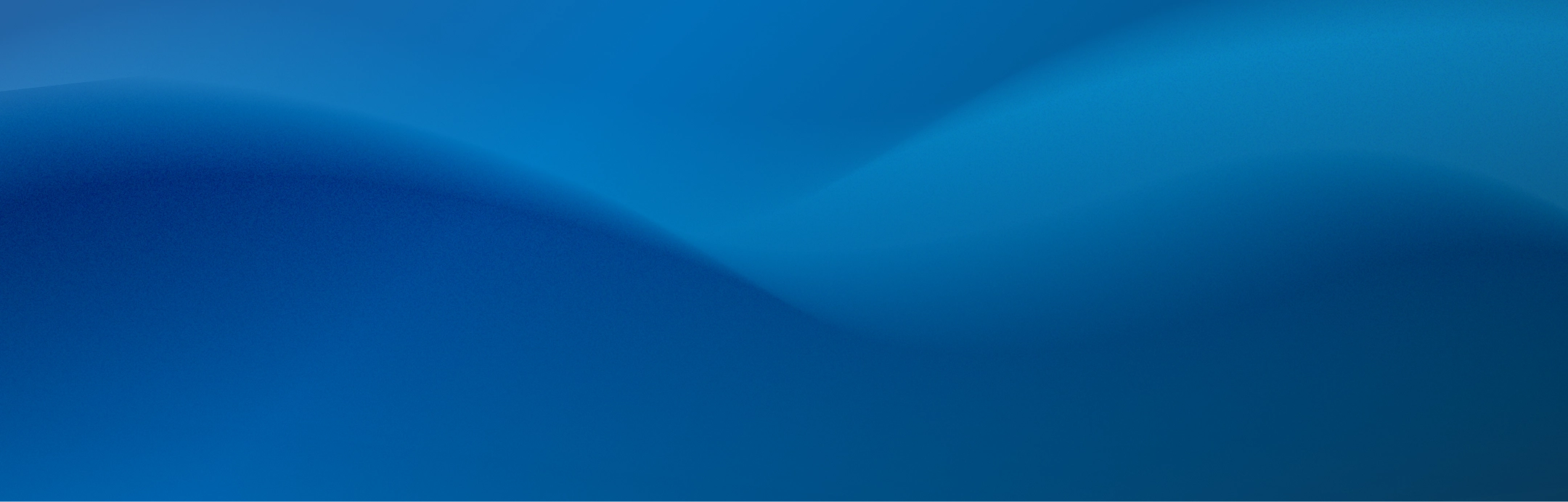
AWWA Articles
Bolton’s woodchip bioreactor: A green solution for nitrate reduction
When the town of Bolton, nestled in New York’s Adirondack Mountains, set out to reduce the nitrates in its wastewater, there were many expensive options to choose from. But they just weren’t viable for the town, a popular tourist destination with about 2,000 year-round residents.
“We were looking for a cost-effective way to reduce nitrates in our effluent,” said Kathleen Suozzo, an engineer working with the town. “The treatment plant, originally built in the 1960s, had been upgraded over the years, but nitrate removal remained a challenge.”
The town, on the western shore of Lake George, faced an added complexity: All wastewater must be discharged into the ground, not surface waters, per New York state regulations.
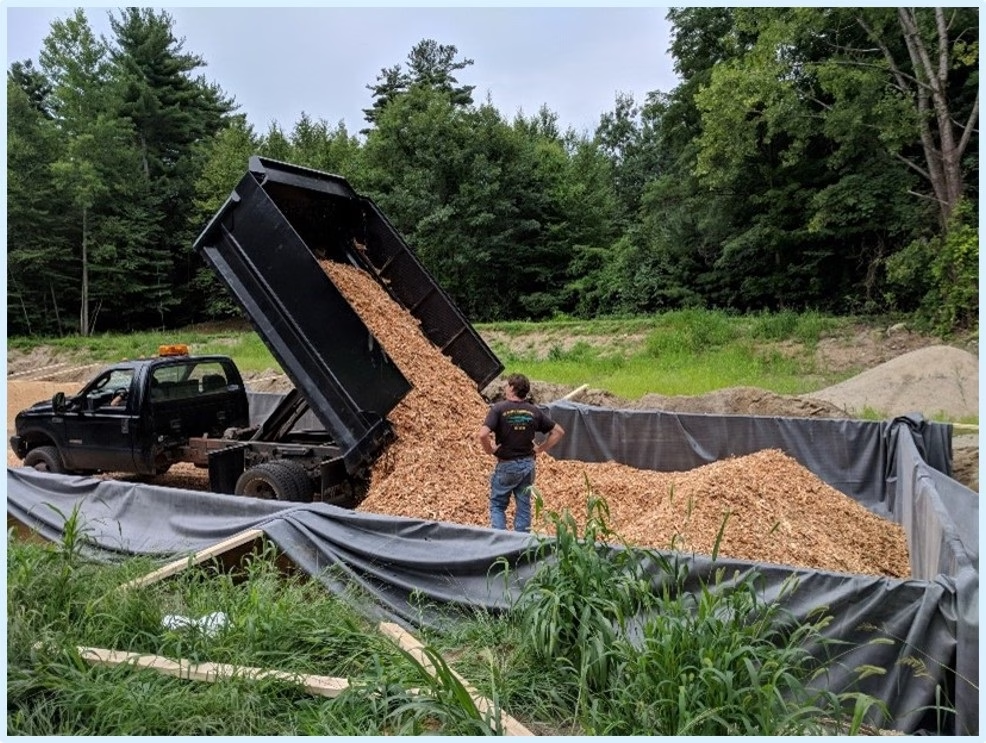
So they turned to an unconventional solution: a woodchip bioreactor.
Inspired by agricultural applications in the Midwest, where researchers at the universities of Iowa and Illinois developed the technology to treat nitrate-rich runoff from fertilized fields, Bolton adapted the concept for municipal wastewater. Bolton is believed to be the first municipality in the United States to do so.
The bioreactor — essentially a “big bathtub,” Suozzo said, with an impermeable pond liner filled with woodchips — allows treated wastewater, low in carbon but high in nitrates, to flow through an anoxic environment. Naturally occurring bacteria use carbon from the woodchips and oxygen from the nitrates, converting them into nitrogen gas, water, and carbon dioxide.
“It’s a passive, green, denitrification process,” said Suozzo, managing principal at Suozzo, Doty and Associates. “And it worked.”
The bioreactor — 20 feet wide, 100 feet long, and 4 feet deep — was constructed by the town’s chief wastewater operator, Matt Coon, with help from the town’s highway department and a local contractor. It was funded with a $50,000 grant from the Lake George Waterkeeper.
Coon described the project as “a big science experiment.”
For example, when solids started to accumulate — because there is no underdrain — Coon thought to try flooding the bioreactor to flush it.
“We were learning as we went,” he said. “There’s no manual for this.”
The flushing worked, so he continued to do it proactively every four to six weeks to keep the bioreactor efficient.
Coon also pulled water samples and sent them to a lab every two weeks to test for effectiveness.
“We were constantly checking on the bioreactor, changing how many gallons per minute were going through it,” said Coon, one of two operators at the plant. “We were going up a couple times a day to check on it.”
For two and a half years, the bioreactor treated up to 100,000 gallons of wastewater daily during the tourist season and 80,000 gallons of wastewater in the low season, reducing nitrate concentrations from 10 mg/L to 3–4 mg/L. However, as the woodchips began to decompose and oxygen levels rose, performance declined.
The town is now preparing for a new phase, thanks in part to a $246,000 Water Quality Improvement Program grant from New York state. They have taken the bioreactor offline while they construct a new one — this time, with concrete walls, a sacrificial front end for easier maintenance (most of the woodchip breakdown occurs in the first 20 feet), and more closely screened woodchips.
“We’ve learned a lot, and we’re applying those lessons,” Suozzo said. She added: The project’s success is a testament to local ingenuity and collaboration between the town board, town supervisor, water plant operators, and Lake George waterkeeper.
“It was all hands on deck.”
Advertisement